It's been an interesting birthday week with a few twists and turns on the construction front. We started the week by spray painting the new foundation walls and then set to work with the mini-digger which couldn't be there until Tuesday (bye bye to another day).
![]() |
Laying out the new footings for the foundation |
Things I've learned throughout the course of the week:
1) The construction world is more akin to a four-day-work-week. It's almost impossible to get five days worth of work out of a given week. Invariably someone can't work, or something's not ready to go, so you lose at least one work day per week. It's pretty frustrating when you're paying about $100/day in overhead costs just to maintain the site, but it's what you deal with. Worth knowing for others however.
2) Our place was built upon not just silty-clay soils, but also a refuse heap. I'm not exactly sure when, but roughly around the turn of the century, our property was used as a bit of a dump pile. As we've been digging down through the soils, we've been uncovering all sorts of interesting things...the most interest of which was an old ink container (intact!) from 12-01-03 from the then-young Diamond Ink Co in the USA. Kinda cool to pull a piece of history like that out of your front yard!
![]() |
Standard "stuff" that's coming out of the ground...mainly broken bottles, pieces of metal (e.g., half a spoon!) |
![]() |
The "gem"/artifact. Hey - eBay says it's worth $30! I'm rich! |
3) Our slab was not built to support a mini-digger. Yep - a mini digger and bobcat managed to mangle the slab. Oh well...just means a bit more fill. At least they nicely dug out the foundations - three days and $3000 later that is... I must admit however, that it was pretty amazing watching him work actually...kind of like machine ballet!
![]() |
A shot of the mini-digger at the front |
![]() |
Mini-digger at rest in the back yard...mushing our 1" thick slab |
![]() |
Job done! |
![]() |
And the end product...with a topping of $275 worth of rock. |

The system uses these Modulogreen units which are recycled ABS plastic and allow one to independently pot plants in a soil medium (which differs from many living wall systems that use moss or something else and easily dry out). Full details are here.
Hard call as it would be a definite "luxury item" in the house...BUT I think it would be spectacular. Decisions, decisions!
These shots give you a sense of what it would look like:
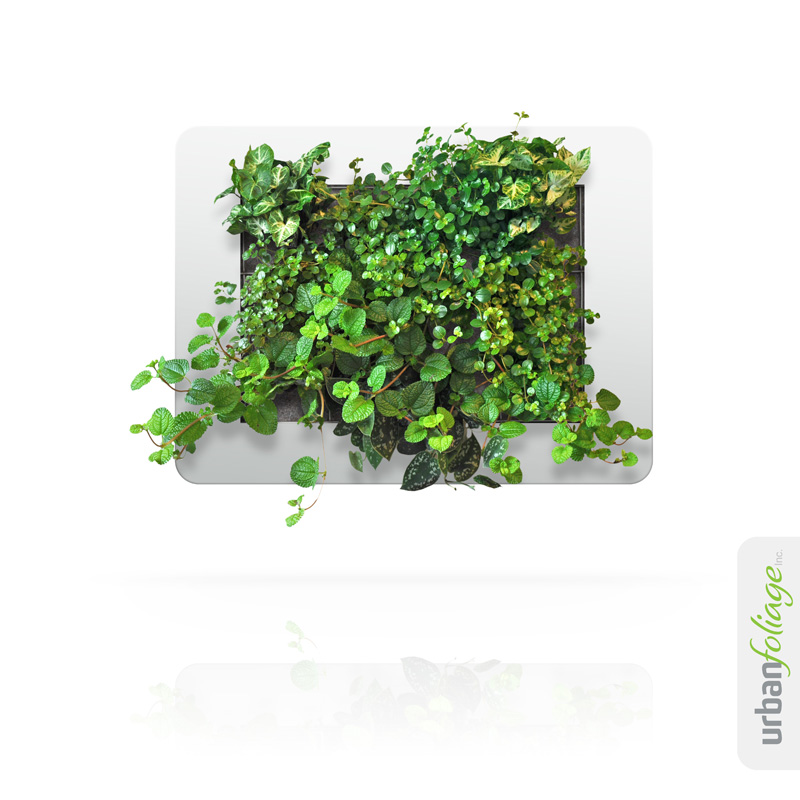
5) Through all the pain of construction, Vancouver does remind me from time to time why it's so amazing out here. This past weekend was pretty spectacular. The weather was between 23 and 28 degrees blue skies for the most part. Kris and I took advantage of the weather and the pre-baby time to enjoy ourselves and had two days where we had some beach time. We also checked out some stores in town, and even began the quest for our new wood slab for our island countertop (more on that one in another post). But with views like this, how can you not love Vancouver?
![]() |
View from English Bay at sunset |
![]() |
Pretty nifty desk from CB2 |
![]() |
Interface FLOR tiles, which I think may be a neat addition to our house |
Other random thoughts...
A) Still mulling over whether to put in a 14" Solatube or not. There's a big hole where the chimney was, and it would nicely illuminate the central space of the house, but it's not an energy efficient thing to do (you're basically shoving an R-5 hole in your roof which should be R-50). BUT conversely, it does add light to the middle of an area that's almost below grade...I think
B) Thinking about doing a wall in brick like this (see below). I'd aim to use the bricks that were reclaimed from the chimney and since they'd be sitting on the slab, the weight shouldn't be an issue (though I'd need to confirm that).
Out of steam for the night...